کوره پاتیلی چیست ؟
کوره القایی یکی از کوره هایی است که تولید فولاد توسط آن انجام می شود این کوره بر اساس میدان مغناطیسی و جریان برق کار می کند , کوره های القایی انواع مختلفی دارند یکی از اصلی ترین انواع آن کوره پاتیلی است که برای ذوب فلزات آهنی و غیر آهنی استفاده می شود . گلنرده سعید ارائه کننده تولیدی حفاظ آکاردئونی ضد سرقت با طرح های مدرن روز در خدمت شماست . برای مشاوره و کسب اطلاعات بیشتر با ما در تماس باشید و یا همراه ما باشید با :
- کوره پاتیلی و کاربرد آن
- هدف استفاده از کوره های پاتیلی
- مزایای کوره های پاتیلی
- مشخصات کوره های پاتیلی
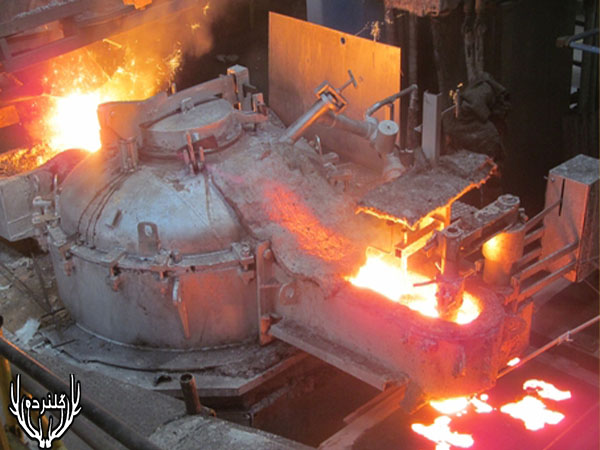
کوره پاتیلی و کاربرد آن
کوره پاتیلی متشکل از پایه فلزی بوده و درون آن سیم پیچ القایی قرار دارد , زمانی که یک جریان متناوب از سیم پیچ عبور می کند یک میدان مغناطیسی در داخل بطری ایجاد شده و این میدان مغناطیسی جریان گردابی را در فلز داخل بطری ایجاد می کند و فلز پس از حرارت دهی ذوب می شود , کوره های پاتیلی برای پالایش فرآیند اولیه تولید فولاد در اغلب کنش های پالایش ثانویه استفاده می شوند , کاربرد و وظیفه آن ها شامل موارد زیر است .
- گرم کردن مجدد فولاد مذاب توسط نیروی الکتریکی
- همگن سازی دما
- ترکیب شیمیایی فولاد با گازشویی
- تشکیل لایه ها و مواد سرباره ای
- اضافه کردن سیم مغزدار و فروآلیاژ ها برای کنترل مواد شیمیایی
- فسفر زدایی و گوگرد زدایی
هدف استفاده از کوره های پاتیلی
از مهم ترین اهداف استفاده از کوره پاتیلی در تصفیه فولاد می توان به , آلیاژ سازی , گوگرد زدایی , اکسیژن زدایی , تنظیم سوپرهیت , حذف هیدروژن , کربن زدایی , حذف عناصر غیر فلزی نامطلوب , بهبود چقرمگی و شکل پذیری , تغییر آخال های غیر فلزی متالوژی ثانویه یا حذف آن و همگن کردن مواد از لحاظ دما و ترکیب شیمیایی توسط گاز خنثی آرگون یا نیتروژن اشاره کرد .
تولیدی درب فرفورژه اینجاست
مزایای کوره های پاتیلی
- امکان ذوب فولاد در مقیاس کوچک
- سرعت بالای ذوب
- کاهش آلودگی
مشخصات کوره های پاتیلی
نوع کوره پاتیلی باز و حرارت تحت اتمسفردر هوای محیط و انجام شده و همزنی مذاب توسط گاز خنثی در آن انجام میگیرد و مانند روش میدرکس بر پایه کوره های قوس الکتریکی , بازوهای نگهدارنده الکترود با قوس الکتریکی کم ساخته شده اند , مصرف انرژی در کوره های پاتیلی نوع LF در واحد فولادسازی MVA30 در تراتس و ماکزیمم توان MW22 و KWH/TON65 است , واحد پاتیل به عنوان واسط بین واحدهای ریخته گری در راستای بهبود فرآیند ریخته گری مداوم عمل کرده و آهک و کک مواد اولیه این بخش است , بوکسیت , کلسیم آلومینات , الکترود , گاز آرگون و فروآلیاژها از قبیل فروسیلیس , فرومنگنز , فروسیلیکو منگنز و …. بسته به گرید تولیدی مصرف می شوند .